Appear ink printing technology, directly contributing to the domestic sanding machines and inkjet printers and other ancillary equipment manufacturers a feast. In particular, the promotion and application of ceramic ink market demand of domestic market demand for nano-materials sand mill to form a strong support, in 2011 sander market was largely monopolized by foreign Netstal and other manufacturers, the price is expensive The outrageous. The 2013 Guangzhou Fair has emerged 4-5 sanding machine manufacturer, to 25 liters of sanding machine, for example, in the 2012 can be sold more than 50 million, but after entering the 2014 price decline directly to 400,000 about 30 liters of sanding machine should be more suitable for large-scale production of ceramic inkjet ink, and has about 300,000 manufacturers offer. Jet mill in ceramic color glaze factory applications are expanding, especially ink pigment powder glaze preliminary processing and printing processing solution used to jet mill.
Traditional solid phase synthesis pigment manufacturing process, material mixing process is basically used to arm screw mixer and coulter mixer, of course, there are some manufacturers use a specific horizontal mixing device, also used to be a ball mill mixing.
Coulter blender machine is mainly used in the finished ceramic pigment and raw material mixing aspects, the common Coulter blenders have 1 ton and 3 tons of two specifications, Coulter blenders mixing time normally required 2-3 hours, with the installation of the required installation lifting platform. Especially raw materials or finished product viscosity is relatively large when using the coulter type mixer at high speed through the tip can break up the lumps of material.
Arms spiral mixer is mainly used for shipping finished ceramic pigment links, with respect to high-speed operation of the tip Coulter blender, screw mixer is suitable for mixing dry powder materials. Mixing time is usually between 2-4 hours, to mix the material processed through the internal rotation of two arms, due to the presence of mixing the bottom corner, production processes usually requires feeding will be one or two bottoms Place the outer loop to mix well.
The mill is from the cylinder, and out of the hollow shaft and the grinding material and some other level of composition, the cylinder is long cylinder, cylinder with grinding, cylinder is of steel manufacturing, there is a steel cylinder liner and fixed, grinding general a steel ball, according to a certain percentage of different diameters and load cylinder, grinding steel section can also be used. Material from the feed device evenly into the mill first warehouse into the compound by the air shaft spiral, the warehouse has ladder liner or corrugated liner, built with a variety of steel ball, rotating cylinder produces centrifugal force to the ball a certain After the height of the fall, have severe impact on the material and abrasive. The material in the first position reached kibble, after single-layer diaphragm plate into the second warehouse, the warehouse lined with flat lining, the steel ball, the material to further grinding. Powder is discharged through the discharge grate plate to complete the grinding operation.
During the rotation of the cylinder, grinding phenomenon have slipped in during the fall to the material to abrasive action, in order to effectively use abrasive, large particle size of the material is generally 20 mesh ground when the grinding body separator cylinder Sec divided into board positions, namely a two-bin, the material into the first position when the ball was crushed, the material into the second position when the steel section of the material for grinding, grinding qualified material discharged from the discharge end of the hollow shaft When small particles of feed material were finely ground, such as sand II slag, coarse fly ash, mill shell or not to set partitions, a single-chamber tube mill, grinding can also be of steel segments.
Raw materials through the hollow journal to be milled into the hollow cylinder, the cylinder built with various diameters grinding media (balls, steel bars or gravel, etc.). When the drum about a horizontal axis at a constant speed of rotation when mounted in the barrel of the media and materials under the effect of centrifugal force and friction, as the cylinder reaches a certain height, when greater than the centrifugal force of its own gravity, then from tube falling or rolling down the inner wall of the projectile, due to impact forces crushed ore. While the mill rotation, grinding media slide mutual
Motion for raw materials also produce abrasive. After grinding the material discharged through the hollow journal.
Ball in the ceramic industry also belongs to dual-use machinery, raw material can be used for milling mix to be used for the finished product refinement process and finished products shipped mixing. Especially the part Glaze ball mill processed product must be used, for example, the black glaze with pigment and part of praseodymium yellow product, quality product performance and processing mill processing fine machining thin significantly different. In addition, the ceramic zirconium iron red pigment in red and aluminum iron and other products, you must use the ball mill mixing for production, zirconium iron red ball milling the ingredients time between 8-12 hours. When used raw mill, ball stone, the proportion of water is one of the key factors, a reasonable ratio can improve milling efficiency, reduce milling time.
Hot Line:
+86-757-86139218
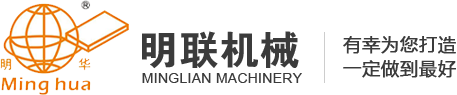